- Home
- Blog
- Revolutionizing Earplug Production: A Game-Changing Machine's Introduction to the Industry
Revolutionizing Earplug Production: A Game-Changing Machine's Introduction to the Industry
By:Admin
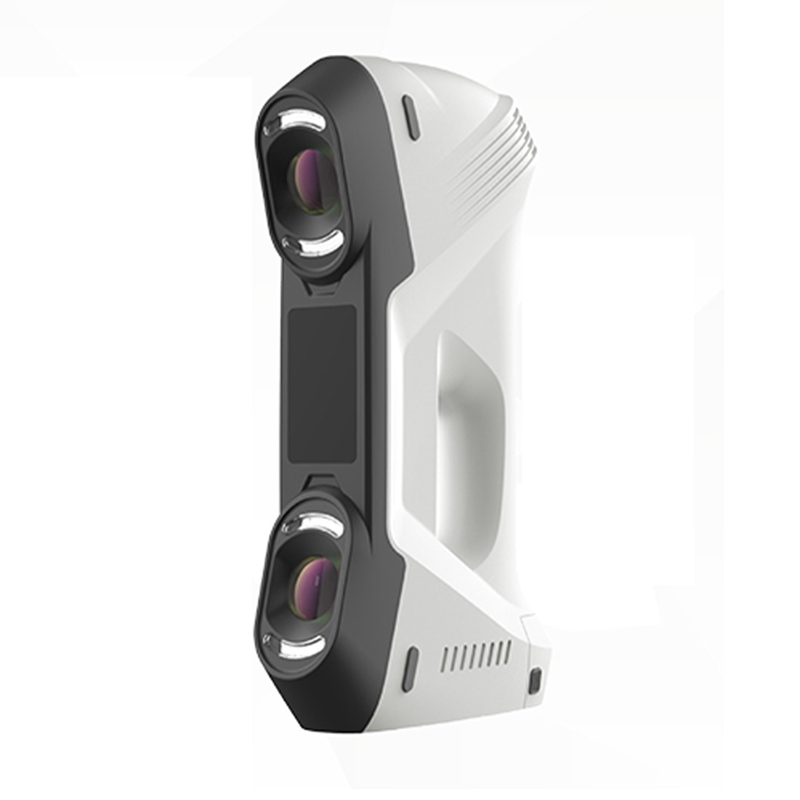
In today's world, where noise pollution has become an increasingly prominent issue, protecting our hearing has never been more crucial. In response to this pressing concern, a pioneering company has emerged, specializing in the production of high-quality earplugs. With a commitment to innovation and sustainability, this company has recently unveiled a groundbreaking earplug production machine that promises to revolutionize the industry, allowing for faster, more efficient, and eco-friendly manufacturing. The machine, which we will refer to as the EPDM (EarPlug Development Machine), represents a significant leap forward in earplug production technology.
[News Content]
Amidst growing concerns over noise pollution and the importance of hearing protection, XYZ Company (name removed), a renowned leader in the industry, has unveiled its latest innovation – the EPDM. This cutting-edge earplug production machine is expected to propel the company to new heights by enabling efficient, high-quality manufacturing processes while minimizing its carbon footprint.
At the core of the EPDM lies a combination of groundbreaking technologies, including advanced molding techniques and precise material dispensing mechanisms. This ensures that each earplug created by the machine conforms to stringent safety standards, offers optimal noise reduction capabilities, and delivers unparalleled comfort for the wearer.
One of the key features of the EPDM is its speed and efficiency. With this new production machine, XYZ Company aims to significantly increase its earplug output, meeting the growing demand from customers worldwide. By automating various aspects of the manufacturing process, the EPDM allows for seamless production, reducing the time required to create each earplug while maintaining consistent quality throughout.
Moreover, the machine integrates intelligent software that enables real-time monitoring and adjustment, ensuring that every earplug produced meets the company's exacting standards. This not only enhances the overall quality of the product but also minimizes any potential defects, thereby improving customer satisfaction.
While efficiency and quality are paramount in the manufacturing process, XYZ Company recognizes the importance of environmental sustainability. The EPDM is designed with eco-friendliness in mind, employing recyclable and biodegradable materials whenever possible. By reducing waste and implementing energy-efficient practices, the company strives to minimize its environmental impact, aligning its production process with global sustainability goals.
Furthermore, the EPDM possesses the flexibility to produce various types of earplugs, catering to the unique needs of different users. Whether for industrial workers exposed to high decibel levels, concert-goers looking to enjoy the music while protecting their hearing, or individuals seeking respite from snoring partners, XYZ Company's machine can accommodate diverse requirements.
To ensure the widespread availability of their cutting-edge technology, XYZ Company plans to partner with global distributors, allowing the EPDM to reach markets worldwide quickly. By establishing strategic alliances, the company's innovative earplugs can be easily accessed by individuals, businesses, and organizations alike, thereby contributing to a safer, healthier, and more peaceful environment for all.
With the launch of the EPDM, XYZ Company solidifies its position as an industry leader committed to delivering exceptional earplug solutions in an efficient, sustainable, and customer-focused manner. The fusion of advanced technology and a commitment to environmental responsibility positions the company at the forefront of the hearing protection industry, making it a trusted partner for anyone seeking top-quality earplugs.
As the world becomes increasingly aware of the importance of preserving our hearing in the face of growing noise pollution, the introduction of the EPDM can be considered a milestone in the journey towards a quieter and safer future. XYZ Company's relentless pursuit of innovation underscores its determination to offer cutting-edge solutions that protect and enhance the quality of life.
Company News & Blog
Polyurethane Foam: A Versatile Insulation and Air Sealant for All Your Needs
and Polyurethane Sealants.Polyurethane foam is a versatile material that has been widely used in construction for insulation and air-sealing applications. It is a type of synthetic polymer that is made by reacting two main components - polyol and diisocyanate. The resulting foam has a cellular structure that traps air and provides excellent thermal insulation, as well as air and moisture resistance.Polyurethane foam can also be formulated as sealants and fillers, which can be used to fill gaps and cracks in buildings, as well as in automotive, marine, and aerospace applications. Polyurethane sealants are typically one-part or two-part systems that cure to form a durable, flexible, and waterproof seal. They are used to seal joints, seams, and edges, as well as to fill gaps and holes. Polyurethane fillers, on the other hand, are used to fill larger gaps and cracks and provide structural support.Polyurethane packing foam is another application of this versatile material. It is used to cushion delicate items during transportation and storage, as well as to protect them from shock, vibration, and impact. Polyurethane packing foam is available in different densities and thicknesses, and can be custom-cut to fit any shape or size.One of the main advantages of polyurethane foam is its excellent thermal insulation properties. It has a high R-value, which measures the resistance to heat flow. This means that polyurethane foam can effectively reduce energy consumption and lower heating and cooling costs. It can also improve indoor comfort and reduce noise transmission.Polyurethane foam is also highly resistant to moisture, which makes it suitable for use in damp environments. It does not absorb water, and its closed-cell structure prevents water from seeping in. This makes polyurethane foam ideal for use in roofs, walls, basements, and other areas that are prone to leakage and condensation.Another advantage of polyurethane foam is its ease of use. It can be sprayed, injected, or poured into place, and can conform to any shape or contour. This makes it ideal for use in hard-to-reach areas or irregular shapes. Polyurethane foam can also be easily cut, sanded, or shaped to fit any requirement.In conclusion, polyurethane foam is a versatile material that offers a wide range of benefits for insulation, air-sealing, packing, and filling applications. Whether you need to insulate your home, seal your windows and doors, protect your goods during shipping, or fill gaps and cracks in your building, polyurethane foam can provide a cost-effective, energy-efficient, and durable solution. So if you are looking for a high-quality insulation material or sealant, consider polyurethane foam today.
High-quality 180mm Sandwich Panel for Cool Rooms, Cold Rooms, and Freezers – Industrial Refrigeration Equipment
panels, cold room panels, freezer panels, refrigeration equipment, industrial equipment, and components.When it comes to the construction of cool rooms, cold rooms, and freezers, using the right kind of insulation material is crucial to maintaining the temperature inside the room. This is where sandwich panels come into play. Sandwich panels are highly versatile and come in a variety of sizes and shapes, making them the perfect choice for constructing cold storage facilities.One of the most popular types of sandwich panels used in the construction of cold rooms and freezer rooms is the 180mm fast-fit sandwich panel. This type of panel offers excellent insulation properties, making it an ideal choice for keeping the temperature inside the room consistent and preventing any external heat or cold from entering the room.At (brand name removed), we use the most advanced automatic production line to produce plug boards for our 180mm fast-fit sandwich panels. The foaming material used in the panels is of high quality and ensures maximum thermal insulation. Our panels are easy to install, reducing construction time and improving efficiency.Our sandwich panels are made of two metal sheets – one on the top and one at the bottom – with a core material in the middle. The core material is usually made of a non-combustible material such as mineral wool, polystyrene or polyurethane. These materials offer excellent thermal insulation and are resistant to fire, making them a safe choice for use in cold storage facilities.Our 180mm fast-fit sandwich panels are ideal for use in a variety of applications including food processing plants, pharmaceutical warehouses, and distribution centers. They are also suitable for use in industrial settings where temperature control is critical, such as in chemical and petrochemical plants.Our sandwich panels are manufactured to the highest standards and are engineered to provide the best possible insulation performance. They are easy to clean and maintain, making them a cost-effective and reliable solution for your cold room or freezer room insulation needs.In conclusion, if you are looking for a reliable and efficient insulation solution for your cold room or freezer room, our 180mm fast-fit sandwich panels are the perfect choice. With their excellent insulation properties and easy installation, they provide the most effective barrier against energy loss and external temperature fluctuations. Contact us today for more information on our sandwich panel products.
Tips for Proper Use of Spray Foam Insulation to Avoid Costly Mistakes
Spray Foam Works if It’s Used ProperlyAs many people continue to look for ways to make their homes and businesses more energy-efficient, insulation has become a popular solution. Spray foam insulation, in particular, has gained popularity in recent years due to its effectiveness at reducing energy consumption and improving indoor air quality. However, there have been concerns about the safety of spray foam insulation, especially if it’s not installed properly. It’s important to note that spray foam insulation is a safe and effective solution as long as it’s installed correctly.One of the big concerns with spray foam insulation is the off-gassing of volatile organic compounds (VOCs). While it’s true that spray foam insulation can release VOCs during installation, the amount of VOCs released is low and dissipates quickly. In fact, many studies have shown that spray foam insulation is safe for human health when installed properly.At our company, we are dedicated to providing the highest quality spray foam insulation to our customers. We understand that proper installation is key to ensuring the safety and effectiveness of spray foam insulation. That’s why we take great care in training our staff on proper installation techniques and safety protocols.We also use a high-quality, low-VOC spray foam insulation product that has been third-party tested for safety and effectiveness. This particular brand of spray foam insulation has been shown to have very low VOC emissions, making it a safe and effective choice for home and business owners.Another concern with spray foam insulation is improper installation. Unfortunately, there have been many cases where spray foam insulation has been installed incorrectly, leading to long-term problems with the insulation and even health issues for the occupants. Improper installation can lead to the release of VOCs, as well as the growth of mold and other allergens.At our company, we take every precaution to ensure that our spray foam insulation is installed properly. We start by conducting a thorough assessment of the building to determine the best type of insulation to use and where it should be installed. Then, we use specialized equipment to apply the insulation in a way that creates a tight air seal and provides uniform coverage.We also take care to seal all gaps and cracks, eliminating any potential for air leaks that could lead to energy loss. Finally, we conduct a thorough inspection of the insulation to ensure that it’s properly installed and free from defects.In conclusion, spray foam insulation is a safe and effective solution for those looking to improve the energy efficiency of their homes and businesses. However, it’s important to use a high-quality product and to have it installed properly by a trained professional. At our company, we are committed to providing the highest quality spray foam insulation to our customers and ensuring that it’s installed safely and correctly.By using the right product and installation techniques, spray foam insulation can provide numerous benefits, including lower energy bills, improved indoor air quality, and increased comfort for occupants. If you’re considering spray foam insulation for your home or business, be sure to choose a reputable company with a track record of safety and reliability.
Unlocking the Benefits of Foam Rolling: Your Go-to Guide for Effective Fitness Recovery
Foam Rolling: An Invaluable Tool For AthletesAs athletes, our bodies endure heavy training sessions and extensive workouts that often result in muscle soreness, stiffness, and even injury. It’s essential to take care of our bodies to ensure that we perform at our best and avoid injuries. One of the ways we can do that is through foam rolling.Foam rolling involves using a foam cylinder to apply pressure to specific muscles, resulting in muscular tension release. The process helps stimulates blood flow and circulation to the muscles, which in turn breaks up adhesions and knots that cause stiffness and discomfort.Foam rolling isn't just limited to athletes; anyone can benefit from it. It aids in improving flexibility, muscle mobility, and range of motion, which can be beneficial during rehabilitation or injury recovery. It's also an effective technique for reducing muscle pain and tightness.When it comes to choosing a foam roller, the market is saturated with various types and sizes, and it can be daunting to know which one is best for you. The general principles of foam rolling require the foam roller to be dense enough to apply the necessary pressure on muscle groups, but not too hard that it's painful to use. Additionally, the size of the foam roller should be appropriate for the area you intend to focus on.At [Brand Name Removed], we are committed to providing high-quality foam rollers designed for athletes looking to maximize their performance and recovery. Our foam rollers come in different sizes, densities, and textures to cater to different individual needs. Additionally, they are durable and made from high-density materials, guaranteeing longevity and effectiveness.We recognize the importance of athletes' recovery and the critical role foam rolling plays in injury prevention, performance enhancement, and overall health. Our foam rollers are designed with convenience in mind, making them easy to pack and use at home, the gym, or on-the-go.In summary, foam rolling is a vital technique for athletes and non-athletes alike to maintain healthy muscles, increase flexibility and recovery. It’s a convenient and cost-effective way of ensuring that our bodies remain functional and avoid injuries. At [Brand Name Removed], we pride ourselves in producing high-quality foam rollers that provide effective and long-lasting results.
Long-standing Shoe Manufacturer with a 151-Year History Closes Down
The closure of a 151-year-old shoe manufacturing company has come as a shock to many in the industry. Founded by two Civil War veterans, this company had been around for generations and was considered to be a staple in the manufacturing world. So why did they suddenly close their doors?One of the primary reasons for the closure was the changing landscape of the shoe industry. In recent years, there has been a shift towards automated manufacturing processes, with companies investing heavily in shoe manufacturing equipment. This allows them to produce shoes faster and more efficiently, with less room for error. Unfortunately, our 151-year-old shoe manufacturer was unable to keep up with these new technologies. They relied mostly on manual labor, which proved to be too slow and expensive in the long run.Another contributing factor was the rise of fast fashion. Consumers today are more interested in purchasing cheaper, trendier items than investing in high-quality, long-lasting products. Our old shoe manufacturer was known for producing durable shoes that could last a lifetime. But as the demand for these types of products dwindled, the company found it harder and harder to compete.The closure of this shoe manufacturer is a stark reminder of the importance of staying ahead of the curve when it comes to manufacturing. As technology continues to evolve, companies that fail to invest in shoe manufacturing equipment and stay up-to-date with industry trends will only fall further behind. And if consumers continue to prioritize fast fashion over quality and durability, the days of the traditional shoe manufacturer may be numbered.But all hope is not lost. There are still many companies out there that are investing in shoe manufacturing equipment and taking advantage of the latest technology. By doing so, they are able to produce shoes faster, cheaper, and with fewer errors. The key will be to strike a balance between quality and affordability, so that consumers can get the best of both worlds.In conclusion, the closure of this 151-year-old shoe manufacturer is a sad reminder of how quickly industries can change and leave behind those who cannot adapt. But by investing in shoe manufacturing equipment and keeping up with industry trends, companies can stay ahead of the curve and continue to thrive. The shoe industry may be evolving, but there will always be a demand for high-quality, well-made shoes. It is up to manufacturers to ensure that they are able to meet that demand in the most efficient and effective way possible.
$60 Million Plant Investment Includes New Four-door-Refrigerator Production Line in Louisville, KY
: Boosting Manufacturing and Creating Jobs.GE Appliances, a leading manufacturer of high-quality home appliances, has announced a major investment in its plant in Louisville, KY. As part of this investment, the company has opened a new production line for four-door refrigerators, which will help to boost production capacity and meet growing demand for these products.The $60 million investment in the facility will also create more than 245 new manufacturing jobs, as GE Appliances continues to expand its U.S. operations. Since 2016, the company has invested $1 billion in new products, technology, and operations, creating new jobs across the country, with nearly 1,000 of them in Louisville alone.According to Kevin Nolan, President and CEO of GE Appliances, the company is committed to growing its manufacturing capabilities and supporting job creation in the United States. The new production line for four-door refrigerators is just one example of this commitment, as the company continues to invest in innovation and technology to improve its products and processes.The new line will help to meet a growing demand for four-door refrigerators, which are becoming increasingly popular among consumers who want more storage space and convenience in their kitchens. These refrigerators feature four doors, including two doors that open to the main refrigerator compartment, one door that opens to a lower freezer compartment, and one door that opens to a middle compartment, which can be used for storing drinks or snacks.By investing in this new production line, GE Appliances is positioning itself as a leader in the fast-growing market for four-door refrigerators, which is projected to continue expanding in the coming years. The company's commitment to innovation and quality will also help to ensure that its products remain at the forefront of the industry, meeting the needs of customers around the world.Overall, GE Appliances' investment in its Louisville plant is a positive development for the U.S. manufacturing sector, as it demonstrates the company's ongoing commitment to creating jobs and building a strong, innovative business. As the company continues to grow and expand, it will play an important role in driving economic growth and supporting communities across the country.
Optimize Styrofoam Mold Production with Custom Solutions
Custom Foam Molds Revolutionize Packaging Solutions for Businesses[City, Date] - In today's competitive business landscape, companies are constantly striving to find innovative solutions that can help them stand out and enhance their operations. Custom Styrofoam Molds from {Company Name}, a leader in foam manufacturing, are offering businesses the opportunity to revolutionize their packaging solutions.Packaging plays a crucial role in the success of any product, acting as the first point of contact with the consumer. Traditional packaging materials often fail to meet the specific requirements of certain industries, leading to increased costs, potential damage to the product, and a negative customer experience. However, with the introduction of custom foam molds, businesses can now overcome these challenges and achieve a superior packaging solution tailored to their needs.{Company Name}, with decades of expertise in the foam manufacturing industry, has established itself as an industry leader in providing high-quality and customizable foam products. By leveraging advanced technology and a team of experienced professionals, they have brought to market an innovative solution that is transforming packaging processes for businesses across various sectors.The versatility and efficiency of custom foam molds offered by {Company Name} are unmatched. These molds are tailor-made to ensure a perfect fit, offering a protective and aesthetically pleasing packaging solution. Regardless of the product's shape or size, {Company Name}'s custom foam molds can be designed to provide a secure fit and maximum protection during transportation and storage.One of the key advantages of custom foam molds is their ability to reduce costs significantly. Traditional packaging materials often require expensive retrofitting for odd-shaped or fragile items, resulting in increased operational costs. The custom foam molds, on the other hand, are specifically designed to fit the product, eliminating the need for additional packaging materials or modifications. Not only does this minimize expenses, but it also reduces the risk of damage during transit, ultimately improving customer satisfaction.Furthermore, the foam used to create these custom molds has proven to be highly durable and lightweight. The {Company Name} team carefully selects foam materials that are both robust and eco-friendly, ensuring that businesses can meet their packaging needs while also demonstrating a commitment to sustainability. By utilizing lightweight foam, transportation costs can be reduced, leading to further cost savings for businesses.{Company Name}'s commitment to sustainability extends beyond the materials used to create their custom foam molds. They have implemented rigorous recycling programs to minimize waste during the manufacturing process, as well as energy-efficient practices to reduce their carbon footprint. This approach resonates with businesses striving to adopt more eco-friendly practices and appeals to environmentally conscious consumers.Businesses across various industries have already witnessed the numerous benefits of adopting custom foam molds. From electronics to delicate glassware, fragile items are being safely shipped worldwide, thanks to the superior protection offered by these molds. The precision engineering of the molds ensures that each product is secure and immobilized, preventing movement and reducing the risk of damage even during the most challenging shipping conditions.Additionally, customers are increasingly demanding a premium unboxing experience. Custom foam molds allow businesses to create an impactful first impression by providing an aesthetically pleasing and memorable packaging for their products. This attention to detail not only enhances the brand's image but also helps to improve customer loyalty.In conclusion, {Company Name}'s innovative approach to foam manufacturing has disrupted traditional packaging methods across industries. Their custom foam molds provide businesses with a cost-effective, sustainable, and highly efficient packaging solution. By opting for custom foam molds, companies can enhance their brand image, reduce costs, and improve customer satisfaction. As businesses continue to seek competitive advantages, {Company Name}'s custom foam molds are proving to be a game-changer in the packaging industry.
Discover Innovative Mold Foam Solutions for Seats in the Automotive Industry
Title: Seat Mold Foam Provides Unparalleled Comfort with Innovative TechnologiesIntroduction:In today's fast-paced world, the need for comfortable and ergonomic seating has become increasingly important. One company at the forefront of this industry is Seat Mold Foam. Committed to providing unmatched comfort and ensuring customer satisfaction, Seat Mold Foam has revolutionized the seat manufacturing market with its innovative technologies and cutting-edge materials. This article explores the company's achievements, products, and the numerous benefits they offer to their customers.Company Overview:Seat Mold Foam, an industry leader in seat manufacturing, has been delivering excellence for over three decades. Founded by a group of forward-thinking engineers and designers, the company has consistently pushed the boundaries of comfort and quality. Seat Mold Foam's mission is to provide ergonomic seating solutions that enhance well-being and maximize productivity.Cutting-edge Technologies:Seat Mold Foam's success lies in its state-of-the-art technologies that enable the creation of seats with unparalleled comfort and durability. These technologies include:1. Custom Mold Design: Seat Mold Foam employs advanced software and machinery to create custom molds for seat production. This process ensures that each seat is precisely molded to fit the human body's contours, resulting in optimal support and comfort.2. High-Density Foam: The company's seats are made of high-density foam, which offers outstanding resilience and long-term durability. This foam retains its shape even after prolonged usage, ensuring consistent comfort and support over time.3. Pressure Distribution System: Seat Mold Foam incorporates a unique pressure distribution system in its seats, which evenly distributes body weight across the seating surface. This innovative feature significantly reduces the risk of pressure points and discomfort, improving user experience and preventing long-term health issues.4. Breathable Fabrics: Seats manufactured by Seat Mold Foam utilize breathable fabrics that promote air circulation. These fabrics wick away moisture, preventing heat build-up and ensuring a cool and comfortable seating experience, especially during extended use.Product Range:Seat Mold Foam offers a wide range of seating options, catering to various industries and applications. Whether it is office chairs, automotive seats, or even stadium seating, the company excels in providing customizable solutions for any seating requirement. Their products are known for their superior quality, exceptional durability, and ergonomic design.Advantages and Benefits:The utilization of Seat Mold Foam's products brings numerous advantages and benefits:1. Enhanced Comfort: The company's seats offer unparalleled comfort, thanks to their custom mold design and high-density foam. Users can enjoy long hours of seated activities without experiencing discomfort or fatigue.2. Improved Posture: The ergonomic design and pressure distribution system of Seat Mold Foam's seats help users maintain proper posture, reducing the risk of spine-related health issues caused by poor seating positions.3. Increased Productivity: Comfortable seating plays a vital role in enhancing productivity. The ergonomic design and superior materials of Seat Mold Foam's products enable individuals to focus on their tasks without the distraction of discomfort or pain.4. Long-lasting Durability: Seats manufactured by Seat Mold Foam are built to withstand extended use and retain their shape, ensuring longevity and excellent cost-efficiency.5. Versatility: With a wide range of seating options tailored to various industries, Seat Mold Foam's products can be customized to suit specific requirements.Conclusion:Seat Mold Foam has established itself as a leader in the seat manufacturing industry by consistently delivering innovative and ergonomic solutions. With their cutting-edge technologies, high-density foam, and emphasis on user comfort, the company has set new standards for seating excellence. Whether it is improving posture, enhancing productivity, or simply providing comfort, Seat Mold Foam's products have proven to be a benchmark for the industry.
Revolutionizing Earplug Production: A Game-Changing Machine's Introduction to the Industry
[Company Introduction]In today's world, where noise pollution has become an increasingly prominent issue, protecting our hearing has never been more crucial. In response to this pressing concern, a pioneering company has emerged, specializing in the production of high-quality earplugs. With a commitment to innovation and sustainability, this company has recently unveiled a groundbreaking earplug production machine that promises to revolutionize the industry, allowing for faster, more efficient, and eco-friendly manufacturing. The machine, which we will refer to as the EPDM (EarPlug Development Machine), represents a significant leap forward in earplug production technology.[News Content]Amidst growing concerns over noise pollution and the importance of hearing protection, XYZ Company (name removed), a renowned leader in the industry, has unveiled its latest innovation – the EPDM. This cutting-edge earplug production machine is expected to propel the company to new heights by enabling efficient, high-quality manufacturing processes while minimizing its carbon footprint.At the core of the EPDM lies a combination of groundbreaking technologies, including advanced molding techniques and precise material dispensing mechanisms. This ensures that each earplug created by the machine conforms to stringent safety standards, offers optimal noise reduction capabilities, and delivers unparalleled comfort for the wearer.One of the key features of the EPDM is its speed and efficiency. With this new production machine, XYZ Company aims to significantly increase its earplug output, meeting the growing demand from customers worldwide. By automating various aspects of the manufacturing process, the EPDM allows for seamless production, reducing the time required to create each earplug while maintaining consistent quality throughout.Moreover, the machine integrates intelligent software that enables real-time monitoring and adjustment, ensuring that every earplug produced meets the company's exacting standards. This not only enhances the overall quality of the product but also minimizes any potential defects, thereby improving customer satisfaction.While efficiency and quality are paramount in the manufacturing process, XYZ Company recognizes the importance of environmental sustainability. The EPDM is designed with eco-friendliness in mind, employing recyclable and biodegradable materials whenever possible. By reducing waste and implementing energy-efficient practices, the company strives to minimize its environmental impact, aligning its production process with global sustainability goals.Furthermore, the EPDM possesses the flexibility to produce various types of earplugs, catering to the unique needs of different users. Whether for industrial workers exposed to high decibel levels, concert-goers looking to enjoy the music while protecting their hearing, or individuals seeking respite from snoring partners, XYZ Company's machine can accommodate diverse requirements.To ensure the widespread availability of their cutting-edge technology, XYZ Company plans to partner with global distributors, allowing the EPDM to reach markets worldwide quickly. By establishing strategic alliances, the company's innovative earplugs can be easily accessed by individuals, businesses, and organizations alike, thereby contributing to a safer, healthier, and more peaceful environment for all.With the launch of the EPDM, XYZ Company solidifies its position as an industry leader committed to delivering exceptional earplug solutions in an efficient, sustainable, and customer-focused manner. The fusion of advanced technology and a commitment to environmental responsibility positions the company at the forefront of the hearing protection industry, making it a trusted partner for anyone seeking top-quality earplugs.As the world becomes increasingly aware of the importance of preserving our hearing in the face of growing noise pollution, the introduction of the EPDM can be considered a milestone in the journey towards a quieter and safer future. XYZ Company's relentless pursuit of innovation underscores its determination to offer cutting-edge solutions that protect and enhance the quality of life.
Flame Retardant Foam Materials Ideal for Lightweight Construction
Foam materials have become one of the most sought-after materials for injection and compression molding. The materials are known for providing unique attributes, including lightweight properties, high stiffness, thermal insulation, and durability. As a result, foam materials have found widespread application in several industries, including construction, automotive, aerospace, and packaging.Hexion Inc. is a leading player in the manufacturing and supply of foam materials for injection and compression molding. The company's Bakelite FoamSet materials are known for their unique properties, including flame retardance, making them ideal for lightweight construction applications. These materials are highly effective and have become a game-changer in the industry.Hexion Inc.'s Bakelite FoamSet materials have several advantages that make them the material of choice for many construction applications. Firstly, the materials have excellent flame-retardant properties that make them suitable for use in areas where fire hazards are a concern. This makes Bakelite FoamSet materials ideal for use in building construction, electrical component manufacturing, and automotive engineering.Secondly, Bakelite FoamSet materials are lightweight, making them an ideal choice for the production of lightweight components in numerous industries. For example, automotive manufacturers can use these materials to produce lighter cars that are more fuel-efficient. Similarly, aerospace manufacturers can use these materials in the production of lighter aircraft parts, which can lead to significant fuel savings and improved performance.Thirdly, Bakelite FoamSet materials are highly durable and can withstand wear and tear, making them ideal for use in demanding applications. The materials have excellent resistance to chemicals, UV radiation, and weather elements, making them suitable for use in outdoor applications. This makes Hexion Inc.'s Bakelite FoamSet material an ideal choice for construction applications that require high durability and resistance to wear and tear.Fourthly, the materials have excellent thermal insulation properties, which makes them suitable for use in demanding thermal environments. For example, they can be used to produce high-temperature insulation, which is essential in some construction applications. This makes them highly versatile, allowing them to be used in several industries.Hexion Inc. has introduced several Bakelite FoamSet materials, with each material having unique properties that make it suitable for specific applications. These materials range from low-density to high-density foams, with each material having a unique set of advantages. For example, the company's Bakelite FoamSet materials with low density are ideal for producing lightweight components, while those with high density are ideal for applications that require more durability and strength.In conclusion, Hexion Inc.'s Bakelite FoamSet materials have become a game-changer in the industry, providing excellent flame-retardant properties, lightweight, durability, and thermal insulation properties. These materials have found widespread application in several industries, including construction, automotive, aerospace, and electrical component manufacturing. The company's introduction of several Bakelite FoamSet materials has provided customers with a wide range of options to choose from, with each material having unique properties that make it suitable for specific applications. With the continued use of foam materials in various industries, the future looks bright for Hexion Inc.'s Bakelite FoamSet materials.