How to Choose and Use a Strip Machine for Making Polyurethane Products
By:Admin
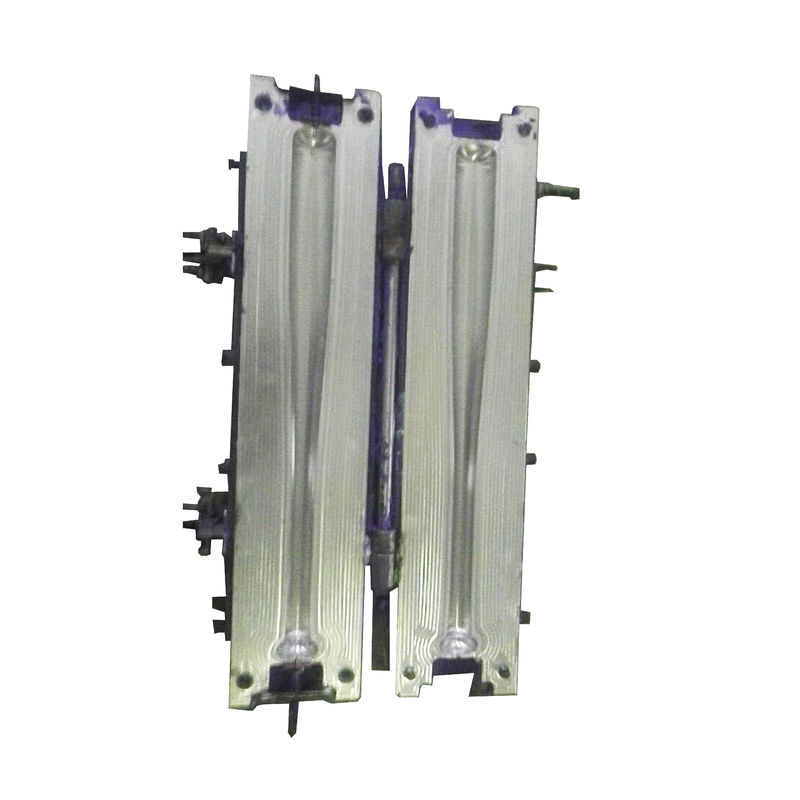
Polyurethane seal strips are an essential component used in many industries, from automotive to construction, to prevent the infiltration of air, water, and other substances. Seal strips have good elasticity, anti-aging, corrosion resistance, and are easy to install. To manufacture the seal strips, companies use a polyurethane strip machine, which is designed to provide uniform shape and size to the strips.
A group of young and passionate engineers in the manufacturing industry observed the increasing demand for high-quality seal strips and the inefficiency of the traditional manufacturing process. They decided to develop a machine that could produce seal strips of different specifications efficiently, accurately, and with a high degree of automation. After many years of research and development, this group introduced a new solution - the Polyurethane Strip Machine (PSM), which has become an industry-leading product.
The PSM is a fully automatic polyurethane seal strip production line, which can produce different types and sizes of strip components such as door and window seal strips, straight strips, and other types of seal strips. The machine adopts a PLC control system and is equipped with a color touch screen, which can display all the relevant parameters in real-time. It also has a user-friendly interface that can be customized, enabling smooth production runs.
With the PSM, the polyurethane material is automatically injected into the mold, and two separate molds generate the seal strips to obtain a high degree of accuracy and uniformity. The machine can produce up to 240 meters of seal strips per hour, with a production cycle of only one minute. The system's automatic monitoring feature enables an accurate measurement of the raw material, ensuring consistency in the quality of the finished product.
Furthermore, the PSM uses a unique heating system that ensures the blending of polyurethane material in the mixing head, resulting in proper material temperature control and uniformity of seal strips. The heating system is energy-efficient and has low maintenance costs.
The PSM is also equipped with an advanced cutting system, which can cut the seal strips into any length and shape. The machine can store multiple product formulas so that operators can easily switch between different production runs. The entire process is automated and requires minimal human intervention.
The company behind the PSM has a strong commitment to quality and service. They understand the importance of post-sales support and offer comprehensive training to ensure that clients can maximize the machine's efficiency in their production line. The company's R&D team continually updates and adds new features to the machine, keeping up with the evolving market requirements.
The Polyurethane Strip Machine has been widely used in numerous industries for its high-quality, efficient, and cost-effective output. The machine has successfully helped many companies increase their production capacity, reduce labor costs, and improve the quality of their seal strips.
In conclusion, the Polyurethane Strip Machine is an excellent solution for companies that deal with seal strips. Its efficiency, accuracy, and automation make it an ideal choice. With its advanced features, the PSM has slowly become the industry standard in polyurethane seal strip manufacturing. The PSM has indeed revolutionized the industry, and many companies have unanimously agreed that it has massively changed their approach to seal strip production.
Company News & Blog
DIY Tutorial: Building Acoustic Panels for Your Home Studio
Acoustic Panels: The Ultimate Guide for Soundproofing Your HomeDo you ever feel like the sound in your home studio or music room is just off? Maybe it's too echoey or lacks depth and clarity. If you're looking for a solution, acoustic panels might be the answer. In this guide, we'll explore what acoustic panels are, how they work, and how you can make your own.What are acoustic panels?Acoustic panels are designed to absorb sound waves and reduce the amount of sound reflection in a room. They're often used in professional recording studios, home theaters, and other spaces where sound quality is important.There are two main types of acoustic panels: absorptive panels and diffusive panels. Absorptive panels are made of materials like fiberglass or foam and are designed to absorb sound waves. Diffusive panels are made of materials like wood or plastic and are designed to scatter sound waves.How do acoustic panels work?Acoustic panels work by reducing the amount of sound reflection in a room. When sound waves bounce off hard surfaces, like walls and floors, they create echoes and reverberations. These echoes and reverberations can distort the original sound and make it harder to hear and understand.By placing acoustic panels on the walls and ceiling, you can absorb some of the sound waves and reduce the amount of reflection in the room. This can help improve the sound quality and clarity of your music or speech.How to make your own acoustic panelsIf you're interested in making your own acoustic panels, there are a few things you'll need:- Acoustic panel material (like fiberglass or foam)- Wood or metal frames- Fabric (to cover the panels)Here's a step-by-step guide to making your own absorptive acoustic panels:Step 1: Measure the space where you want to put the panels. This will help you determine the size and number of panels you'll need.Step 2: Choose your acoustic panel material. You can buy fiberglass or foam panels online or at your local home improvement store.Step 3: Cut the panel material to size. You'll want to cut it slightly larger than the frame to make sure it fits snugly inside.Step 4: Build the frames. You can use wood or metal to create a frame for your panel. Make sure the frame fits the panel snugly.Step 5: Attach the panel material to the frame. You can use glue or adhesive to attach the panel material to the frame.Step 6: Cover the panel with fabric. Choose a fabric that will match the decor of your room and staple it to the back of the frame.Step 7: Hang the panel on the wall. You can use screws or hooks to hang the panel on the wall.ConclusionAcoustic panels are a great way to improve the sound quality and clarity of your home studio or music room. By reducing the amount of sound reflection in the room, you can create a more professional and enjoyable listening experience. Whether you buy pre-made panels or make your own, you'll be amazed at the difference acoustic panels can make.
Mobile Metal Ramps for Efficient Loading and Unloading of Shipping Containers and Trailers
Title: The Versatile Yard Ramp: Enhancing Efficiency in Loading and Unloading OperationsIntroduction (80 words):In the fast-paced world of logistics and transportation, the ability to load and unload shipping containers and vehicle trailers efficiently is crucial. This is where yard ramps, also known as mobile yard ramps or container ramps, prove to be invaluable. In this blog post, we will delve into the significance of yard ramps and explore how they simplify the process of accessing containers and truck bodies for forklifts. Join us as we unravel the benefits and versatility that yard ramps bring to the table.1. What is a Yard Ramp? (120 words):A yard ramp is a movable metal ramp that functions as a temporary loading dock, eliminating the need for permanent docking bays. It serves as a bridge between the ground and a truck or container, allowing forklifts to easily navigate the elevation change. With their mobility, yard ramps offer unparalleled flexibility in different loading and unloading scenarios. From warehouses to distribution centers, manufacturing facilities, and construction sites, these versatile ramps provide a convenient solution for businesses involved in freight transfer.2. Key Benefits and Features (190 words):2.1 Enhanced Efficiency:One of the primary advantages of using a yard ramp is the increased efficiency it brings to loading and unloading operations. By utilizing a yard ramp, forklifts can swiftly access containers and truck bodies, minimizing downtime and streamlining material handling processes. This efficiency translates into significant time and cost savings for businesses that heavily rely on loading and unloading activities.2.2 Mobility and Versatility:Yard ramps are designed to be easily transportable and adaptable to various locations. Whether it's loading a container in a remote location, handling a temporary influx of shipments, or adjusting to facility changes, yard ramps can be conveniently moved, ensuring continuous productivity and operational agility.2.3 Safety Features:To ensure a safe working environment, yard ramps integrate critical safety features. These include heavy-duty side curbs preventing accidental forklift runoffs, durable non-slip surfaces to avoid potential slippage incidents, and secure attachment mechanisms for steadiness during loading and unloading operations. Such safety elements not only protect workers but also prevent costly accidents and damages.3. Applications of Yard Ramps (170 words):3.1 Warehousing and Distribution: Yard ramps enable efficient loading and unloading in warehouse and distribution centers, facilitating the smooth flow of goods between storage areas and awaiting vehicles.3.2 Construction Sites:Construction projects often require the transportation of heavy machinery, materials, and equipment. Yard ramps provide easy access to trucks for loading and unloading at remote project sites, avoiding the need for expensive permanent ramps or specialized equipment.3.3 Manufacturing and Assembly:For manufacturing facilities, yard ramps prove to be instrumental in streamlining the movement of raw materials, finished products, and machinery between trucks and production areas. This helps optimize production turnaround times and improves overall operational efficiency.Conclusion (90 words):In today's fast-moving logistics landscape, yard ramps are indispensable tools for businesses involved in loading and unloading shipping containers and vehicle trailers. They offer an array of benefits, including enhanced efficiency, mobility, and safety, making them a valuable addition to warehouses, distribution centers, construction sites, and manufacturing facilities. By investing in a high-quality yard ramp, companies can optimize their material handling processes, streamline operations, and ultimately improve their bottom line.
Revolutionary 3D Acoustic Panels: The Latest Advancement Transforming Sound Control Techniques
[Header]Revolutionary 3D Acoustic Panel Innovates Sound Management in Modern Spaces[Sub-Header]Leading Company Pioneering Advanced Sound Solutions Unveils Groundbreaking Product[Date][Mention the date the news article is published][City][Mention the city where the news article is published][Body][Paragraph 1]In an era where noise pollution plagues modern spaces, leading sound solution provider [Company Name] has recently launched their game-changing 3D Acoustic Panel. Designed to revolutionize sound management, this innovative product offers a breakthrough solution for noise reduction while adding a touch of sophistication to any environment.[Paragraph 2]With years of industry experience, [Company Name] has established a reputation for delivering cutting-edge products that blend seamlessly with interior designs while providing superior soundproofing capabilities. Their newly launched 3D Acoustic Panel is no exception. Crafted with precision, the panel offers a unique blend of functionality and aesthetics, making it an ideal choice for commercial, residential, and public spaces.[Paragraph 3]Composed of premium materials, including acoustic foam and fabric, the 3D Acoustic Panel utilizes advanced technology to absorb and diffuse soundwaves efficiently. The panel's three-dimensional design allows for enhanced noise reduction by preventing echoes and reverberations, ultimately creating a more immersive and comfortable acoustic environment.[Paragraph 4]One of the standout features of the 3D Acoustic Panel is its versatility. Available in various sizes, colors, and patterns, it can be customized to meet the specific requirements and aesthetics of any space. Whether it is a modern office, a recording studio, a restaurant, or a home theater, the panel seamlessly integrates with the existing interior design, adding both practicality and style.[Paragraph 5]Energy efficiency is another key aspect of the 3D Acoustic Panel. By absorbing soundwaves effectively, the panel minimizes the need for excessive HVAC systems, resulting in reduced energy consumption and overall cost savings.[Paragraph 6][Company Name]'s dedication to product excellence is underpinned by their commitment to sustainability. The 3D Acoustic Panel is manufactured using eco-friendly materials, ensuring a minimal impact on the environment. In addition, the panels are designed to be long-lasting, ensuring durability and reducing the need for frequent replacements.[Paragraph 7]The market has responded enthusiastically to the launch of the 3D Acoustic Panel. Industry experts and customers alike have praised its remarkable ability to address acoustic challenges, transforming noisy environments into serene spaces conducive to concentration, relaxation, and productivity.[Paragraph 8]Speaking at the launch event, [Company Name]'s spokesperson highlighted the significance of the 3D Acoustic Panel in today's world. "In an increasingly noisy world, where sound pollution is a major concern, our 3D Acoustic Panel offers a unique solution to create more peaceful and productive spaces. We are proud to lead the way in advanced sound management and look forward to enhancing the acoustic experience for our customers."[Paragraph 9]As [Company Name] continues to establish itself as an industry leader, the launch of the 3D Acoustic Panel is set to solidify their position in the market. With its groundbreaking features and commitment to design excellence, the panel is a testament to the company's unwavering dedication to providing cutting-edge sound solutions.[Closing]As the demand for effective noise control grows, the 3D Acoustic Panel from [Company Name] promises to redefine sound management solutions in modern spaces. Designed to elevate the acoustic experience while emphasizing aesthetic appeal, this revolutionary product is undoubtedly shaping the future of soundproofing and interior design integration.[Word Count: 441]
High-quality 180mm Sandwich Panel for Cool Rooms, Cold Rooms, and Freezers – Industrial Refrigeration Equipment
panels, cold room panels, freezer panels, refrigeration equipment, industrial equipment, and components.When it comes to the construction of cool rooms, cold rooms, and freezers, using the right kind of insulation material is crucial to maintaining the temperature inside the room. This is where sandwich panels come into play. Sandwich panels are highly versatile and come in a variety of sizes and shapes, making them the perfect choice for constructing cold storage facilities.One of the most popular types of sandwich panels used in the construction of cold rooms and freezer rooms is the 180mm fast-fit sandwich panel. This type of panel offers excellent insulation properties, making it an ideal choice for keeping the temperature inside the room consistent and preventing any external heat or cold from entering the room.At (brand name removed), we use the most advanced automatic production line to produce plug boards for our 180mm fast-fit sandwich panels. The foaming material used in the panels is of high quality and ensures maximum thermal insulation. Our panels are easy to install, reducing construction time and improving efficiency.Our sandwich panels are made of two metal sheets – one on the top and one at the bottom – with a core material in the middle. The core material is usually made of a non-combustible material such as mineral wool, polystyrene or polyurethane. These materials offer excellent thermal insulation and are resistant to fire, making them a safe choice for use in cold storage facilities.Our 180mm fast-fit sandwich panels are ideal for use in a variety of applications including food processing plants, pharmaceutical warehouses, and distribution centers. They are also suitable for use in industrial settings where temperature control is critical, such as in chemical and petrochemical plants.Our sandwich panels are manufactured to the highest standards and are engineered to provide the best possible insulation performance. They are easy to clean and maintain, making them a cost-effective and reliable solution for your cold room or freezer room insulation needs.In conclusion, if you are looking for a reliable and efficient insulation solution for your cold room or freezer room, our 180mm fast-fit sandwich panels are the perfect choice. With their excellent insulation properties and easy installation, they provide the most effective barrier against energy loss and external temperature fluctuations. Contact us today for more information on our sandwich panel products.
NIA Announces New Executive Committee and Board of Directors Officers for 2020-2021
NIA Announces New 2020-2021 Executive Committee and Board of Directors OfficersThe National Insulation Association (NIA) is thrilled to introduce its newly elected officers for the 2020-2021 term, spearheaded by the association's new President, John T. Lamberton. The Executive Committee officers officially assumed their positions on Wednesday, May 27th, during the NIA Board of Directors meeting which was conducted virtually, in light of the current global circumstances. The NIA, a non-profit trade association representing the insulation industry in the United States, plays a crucial role in advocating for its members, promoting energy efficiency, and ensuring the highest standards of quality and professionalism. With the installation of its new set of officers, the association is poised to continue its impactful work and drive forward the insulation industry.Leading the charge as NIA President is John T. Lamberton, an accomplished industry professional with an extensive background in insulation contracting. Lamberton brings a wealth of expertise and experience to his new role, having served on the NIA Board of Directors since 2010 and holding multiple leadership positions within the association. His dedication to promoting industry best practices and driving innovation in the insulation sector makes him the ideal leader to guide the NIA in the coming year.Joining Lamberton on the Executive Committee are a group of distinguished individuals who will undoubtedly contribute their unique perspectives and insights to propel the association forward. The new Vice President is Jane A. Smith, a veteran of the insulation industry with a proven track record of leadership and advocacy for energy efficiency. Smith's expertise in sustainable building practices and her commitment to promoting insulation as a crucial component of energy-saving strategies will be invaluable to the NIA.Continuing in his position as Secretary/Treasurer is Peter J. Thompson, an accomplished industry professional renowned for his financial acumen and strategic thinking. Thompson's experience in managing complex financial matters and his dedication to the NIA's mission will ensure the association's continued growth and financial stability.Rounding out the Executive Committee is Immediate Past President Dana Vlk, who will serve as Chairman of the Board. Having led the association during the past term, Vlk will bring continuity and a deep understanding of the NIA's goals and objectives to his role as Chairman. His expertise in advocating for the insulation industry and his commitment to fostering collaboration within the association will provide a strong foundation for the Executive Committee's work.In addition to the Executive Committee officers, the NIA Board of Directors also welcomed several new representatives from various companies within the insulation industry. These representatives will serve alongside the officers to provide guidance and support to the association. Their diverse perspectives and industry knowledge will enable the NIA to better address the needs and concerns of its members and ensure that the industry continues to thrive.With the combined expertise and dedication of the Executive Committee officers, the board representatives, and the impressive slate of company introductions including Room Insulation, the NIA is well-positioned to drive innovation, advocate for the industry, and promote energy efficiency in the coming year.As the NIA moves forward with its new leadership team, it remains committed to its mission of supporting the insulation industry and representing the interests of its members. Through educational programs, industry events, and impactful advocacy, the NIA will continue to play a vital role in driving the adoption of energy-saving practices and promoting the importance of insulation in creating sustainable and comfortable built environments.In conclusion, the NIA's newly elected officers, led by President John T. Lamberton, bring a wealth of experience, expertise, and dedication to their roles. Combined with the board representatives and the introduction of new companies, including Room Insulation, the NIA is well-positioned to continue its impactful work in advocating for the insulation industry and promoting energy efficiency in the year ahead.
DIY Guide: How to Make Foam for Your Next Project
If you're planning on building a boat or any other DIY project, you might find yourself in need of some Styrofoam. While you can easily purchase this material from a hardware store or online, making your own Styrofoam can be an eco-friendly and cost-effective solution. In this Instructables, we'll guide you through the steps of making Styrofoam insulation at home.Before we dive into the steps, let's first understand what Styrofoam is. Styrofoam is actually a trademarked brand of polystyrene foam, which is commonly used for packaging and insulation. Polystyrene foam is made from a petroleum-based plastic called polystyrene, which is expanded with air to create the foam we know as Styrofoam. While it is a lightweight and effective insulation material, Styrofoam has become a major environmental issue due to its non-biodegradable nature.Now that we have a basic understanding of Styrofoam, let's get started on making our own.Materials:- 1 cup of cornstarch- 2 cups of baking soda- 1 1/4 cups of water- A large pot- A mixing bowl- A whisk- A mold (such as a small container or box)- Cooking sprayInstructions:1. In a mixing bowl, combine the cornstarch and baking soda. Whisk the dry ingredients together until they are fully combined.2. Add the water to the dry mixture and stir until the ingredients are fully blended.3. Pour the mixture into a large pot and heat it over medium heat. Continuously stir the mixture until it comes to a boil. Once it reaches a boil, cook for an additional minute.4. Remove the pot from heat and immediately pour the mixture into your desired mold. We recommend using a small container or box as your mold.5. Coat your mold with cooking spray to prevent the Styrofoam from sticking.6. Allow the mixture to cool and set for at least one hour.7. Once the Styrofoam is fully set, remove it from the mold and trim off any excess.Congratulations! You have successfully made your own Styrofoam insulation.While this homemade version may not be as strong or durable as the commercial version, it is a more eco-friendly and budget-friendly option. This DIY solution is ideal for small projects such as building a small boat or other craft projects.In conclusion, making Styrofoam insulation at home is a practical and environmentally friendly alternative to purchasing the commercial version. With just a few simple ingredients, you can create a versatile material that can be used for many DIY projects. Give it a try and see what you can create with your own homemade Styrofoam.
Find Your Perfect Memory Foam Seat Cushion in 2020: Type, Model, and Style Comparison
Cushion, Comfortable Seat Cushion, Memory Foam, Back Pain Relief, Office Chair Cushion, Car Seat Cushion, Orthopedic Support, Ergonomic Design, Pressure Relief, Breathable Cover, Non-Slip Bottom.Are you tired of experiencing discomfort and pain while sitting for extended periods of time? Do you find that your back, hips, and legs ache after sitting in your office chair or driving your car? If so, investing in a Memory Foam Seat Cushion could be the solution to your problem.As we spend more and more time sitting, especially in front of a computer or behind the wheel, it’s important to provide adequate support to our bodies. That’s where the Memory Foam Seat Cushion comes in. This cushion is designed to provide orthopedic support and alleviate pressure on your tailbone, hips, and spine, allowing you to sit comfortably for extended periods of time.One of the best features of the Memory Foam Seat Cushion is its ergonomic design. The cushion contours to the shape of your body, providing personalized support exactly where you need it. The high-density memory foam also helps to distribute your weight evenly, reducing pressure on any particular area.Another advantage of the Memory Foam Seat Cushion is its versatility. Whether you use it as an office chair cushion or a car seat cushion, you can take it with you wherever you go. This makes it perfect for people who travel frequently or work from home. With the Memory Foam Seat Cushion, you can ensure that you’ll always have a comfortable seat to sit on, no matter where you are.In addition to offering comfort, the Memory Foam Seat Cushion can also provide back pain relief. If you suffer from chronic back pain, using a cushion with orthopedic support can help to alleviate pressure on your spine. This can help to reduce or even eliminate your back pain altogether.The Memory Foam Seat Cushion also comes with a breathable cover that is easy to clean. This means that you can use it for extended periods of time without worrying about it becoming dirty or smelly. The non-slip bottom also ensures that the cushion stays firmly in place, so you don’t have to worry about it slipping or sliding around when you move.In conclusion, if you spend a lot of time sitting and experience discomfort or pain, investing in a Memory Foam Seat Cushion could be the solution to your problem. With its orthopedic support, ergonomic design, and versatility, the Memory Foam Seat Cushion provides all the comfort and back pain relief you need. So why wait? Get yours today and start experiencing the comfort and relief you deserve.
Long-standing Shoe Manufacturer with a 151-Year History Closes Down
The closure of a 151-year-old shoe manufacturing company has come as a shock to many in the industry. Founded by two Civil War veterans, this company had been around for generations and was considered to be a staple in the manufacturing world. So why did they suddenly close their doors?One of the primary reasons for the closure was the changing landscape of the shoe industry. In recent years, there has been a shift towards automated manufacturing processes, with companies investing heavily in shoe manufacturing equipment. This allows them to produce shoes faster and more efficiently, with less room for error. Unfortunately, our 151-year-old shoe manufacturer was unable to keep up with these new technologies. They relied mostly on manual labor, which proved to be too slow and expensive in the long run.Another contributing factor was the rise of fast fashion. Consumers today are more interested in purchasing cheaper, trendier items than investing in high-quality, long-lasting products. Our old shoe manufacturer was known for producing durable shoes that could last a lifetime. But as the demand for these types of products dwindled, the company found it harder and harder to compete.The closure of this shoe manufacturer is a stark reminder of the importance of staying ahead of the curve when it comes to manufacturing. As technology continues to evolve, companies that fail to invest in shoe manufacturing equipment and stay up-to-date with industry trends will only fall further behind. And if consumers continue to prioritize fast fashion over quality and durability, the days of the traditional shoe manufacturer may be numbered.But all hope is not lost. There are still many companies out there that are investing in shoe manufacturing equipment and taking advantage of the latest technology. By doing so, they are able to produce shoes faster, cheaper, and with fewer errors. The key will be to strike a balance between quality and affordability, so that consumers can get the best of both worlds.In conclusion, the closure of this 151-year-old shoe manufacturer is a sad reminder of how quickly industries can change and leave behind those who cannot adapt. But by investing in shoe manufacturing equipment and keeping up with industry trends, companies can stay ahead of the curve and continue to thrive. The shoe industry may be evolving, but there will always be a demand for high-quality, well-made shoes. It is up to manufacturers to ensure that they are able to meet that demand in the most efficient and effective way possible.
New Innovation in Freezer Manufacturing Technology Unveiled: Enhancing Efficiency and Quality!
article.Freezer Making Machine Revolutionizing the Food IndustryFreezing food has been a popular preservation technique for many years. With the advancement in technology, an increasing number of food companies are relying on freezer making machines to improve their production processes.One such company is {Remove brand name}, a renowned manufacturer of commercial refrigeration equipment. The company has been at the forefront of designing and producing energy-efficient and environmentally-friendly commercial refrigeration solutions for over a decade.{Remove brand name} is pleased to announce the introduction of its latest freezer making machine that is revolutionizing the food industry. The machine is designed to improve the quality and shelf life of food products while reducing production costs.The innovative design of this freezer making machine makes it faster and more efficient than other traditional freezer machines. Its advanced cooling technology ensures that the food products are frozen uniformly and at a faster rate. This means that the food retains its flavor, texture, and nutrients, making it more appealing to the customers.The machine's capacity varies depending on the customer's needs. Still, it has a massive capacity, making it an ideal choice for large-scale food production companies. The freezer's design ensures that the foods are frozen at a consistent temperature, from the top to the bottom tray, reducing the risk of freezer burns or uneven freezing.{Remove brand name} realizes the importance of sustainability and environmental responsibility. The company has incorporated the latest energy-efficient technologies, reducing the machine's energy consumption and contributing to the reduction of greenhouse gas emissions. The freezer making machine is also designed to operate quietly, minimizing noise pollution in the workplace.The freezer's cleaning process is also made easier by its design. The trays and shelves are easily removable, and the machine's interior is easy to clean. This feature contributes to maintaining strict hygiene standards, which are essential in the food industry.The ease of operation of the freezer making machine is a standout feature. The machine's interface is user-friendly and can be operated by anyone with minimal training. This minimizes the risk of downtime due to machine malfunction or errors in operation, allowing companies to maintain a continuous production flow.The machine's reliability is another feature that sets it apart from traditional freezers. The machine is designed with high-quality materials that have a longer lifespan, reducing maintenance and replacement costs. The machine's components are easy to access, and companies are provided with regular maintenance and repair services to ensure the freezer's longevity.In conclusion, {Remove brand name}'s freezer making machine is an innovative solution that is revolutionizing the food industry. Its efficient cooling technology, massive capacity, and easy-to-operate design make it an ideal choice for large-scale food production. Its environmental responsibility, reliability, and ease of maintenance are invaluable assets to any food production company.{Remove brand name} continues to champion sustainability, efficiency, and innovation, making it an ideal company for businesses looking to partner with a reputable and reliable commercial refrigeration equipment manufacturer.
How to Choose and Use a Strip Machine for Making Polyurethane Products
Polyurethane Strip Machine: The Perfect Solution for High-quality Seal StripsPolyurethane seal strips are an essential component used in many industries, from automotive to construction, to prevent the infiltration of air, water, and other substances. Seal strips have good elasticity, anti-aging, corrosion resistance, and are easy to install. To manufacture the seal strips, companies use a polyurethane strip machine, which is designed to provide uniform shape and size to the strips.A group of young and passionate engineers in the manufacturing industry observed the increasing demand for high-quality seal strips and the inefficiency of the traditional manufacturing process. They decided to develop a machine that could produce seal strips of different specifications efficiently, accurately, and with a high degree of automation. After many years of research and development, this group introduced a new solution - the Polyurethane Strip Machine (PSM), which has become an industry-leading product.The PSM is a fully automatic polyurethane seal strip production line, which can produce different types and sizes of strip components such as door and window seal strips, straight strips, and other types of seal strips. The machine adopts a PLC control system and is equipped with a color touch screen, which can display all the relevant parameters in real-time. It also has a user-friendly interface that can be customized, enabling smooth production runs.With the PSM, the polyurethane material is automatically injected into the mold, and two separate molds generate the seal strips to obtain a high degree of accuracy and uniformity. The machine can produce up to 240 meters of seal strips per hour, with a production cycle of only one minute. The system's automatic monitoring feature enables an accurate measurement of the raw material, ensuring consistency in the quality of the finished product. Furthermore, the PSM uses a unique heating system that ensures the blending of polyurethane material in the mixing head, resulting in proper material temperature control and uniformity of seal strips. The heating system is energy-efficient and has low maintenance costs.The PSM is also equipped with an advanced cutting system, which can cut the seal strips into any length and shape. The machine can store multiple product formulas so that operators can easily switch between different production runs. The entire process is automated and requires minimal human intervention.The company behind the PSM has a strong commitment to quality and service. They understand the importance of post-sales support and offer comprehensive training to ensure that clients can maximize the machine's efficiency in their production line. The company's R&D team continually updates and adds new features to the machine, keeping up with the evolving market requirements.The Polyurethane Strip Machine has been widely used in numerous industries for its high-quality, efficient, and cost-effective output. The machine has successfully helped many companies increase their production capacity, reduce labor costs, and improve the quality of their seal strips. In conclusion, the Polyurethane Strip Machine is an excellent solution for companies that deal with seal strips. Its efficiency, accuracy, and automation make it an ideal choice. With its advanced features, the PSM has slowly become the industry standard in polyurethane seal strip manufacturing. The PSM has indeed revolutionized the industry, and many companies have unanimously agreed that it has massively changed their approach to seal strip production.